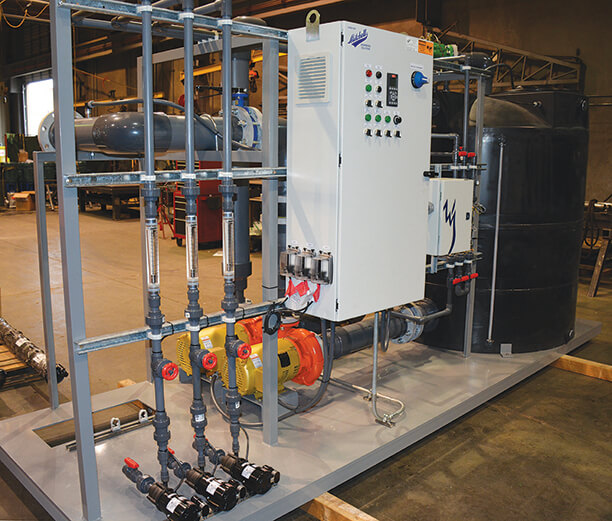
This custom mixing station that MLS Packaged Systems engineers designed and built for WaterTec, is a highly-efficient, VFD-controlled component, integral to irrigating greenhouse crops such as tomatoes, cucumbers, peppers and more. The station blends recycled, excess water, which was not absorbed by the plants with treated fresh water for use in the next irrigation cycle. In the mixing tank, fertilizers are added as a balancing acid to regulate the PH of the water to optimum levels. The water is then pumped from the tank, passing through a series of media filters, and out to the greenhouse.
The frequency of station operation is determined by a Growth Management System that constantly monitors the amount of sunlight, greenhouse temperature and humidity, while measuring the amount of water and fertilizer returning from the plants.
The amount of fertilizer in the outgoing water cycle is regulated using electrical conductivity (EC) sensors located downstream of the mixing tank. The treated water will have a consistent low level of conductivity due to the lack of impurities in the water. Adding fertilizers to the water raises the EC. The grower determines the optimum EC level when selecting the fertilizer mix.
Three to seven fertilizer injector pumps cycle on and off to maintain the fertilizer levels at the correct proportions, all this controlled by the Growth Management System. The outgoing PH is monitored by sensors installed downstream of the mixing tank, and activate the acid pump as needed to maintain the selected set-point. A target PH for tomatoes as an example is around 5.
MLS Packaged Systems advance the growing process enabling a continuous, robust crop cycle, whatever the crop. Operational accessibility and flexibility is a key attribute of MLS custom packaged systems.
–Michael Watterson
MLS Product Manager, Packaged Systems