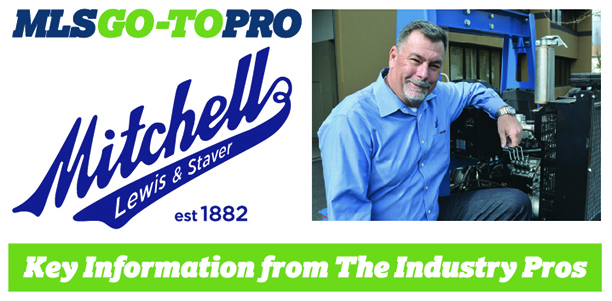
Peter M Albanese
Vertical Turbine Product Manager
Mitchell, Lewis & Staver Company
Determining overall plant efficiency (OPE) in deep well vertical turbine pumps (VTP’S) (often referred to as “wire to water” efficiency) is essential in our design process for VTP’s at MLS. The OPE determines what the end user will pay in dollars to run his pump. The higher this number is in efficiency percentage, the lower those payments will be.
Pumping plant field efficiency tests are conducted to determine the OPE of a system. This number will help an end user decide whether or not to repair or replace his current system. The power savings often enough will pay for a new system within a few years.
Let’s look at some basic terms we use:
Power can be measured both mechanically and electrically.
Mechanically, power is typically expressed as horsepower (HP). One HP is the power required to lift 33,000 lbs one foot in one minute or 550 lbs one foot in one second.
Electrical power is measured in watts
1000 watts = 1 kilowatt
1 kilowatt = 1.34 HP
1 HP = .746 Kilowatts
Pump HP = GPM x Total head (in feet) / 3960 x hydraulic eff
Pumps and motors, like all machines, cannot convert all of the power supplied to them as useful work.Losses occur from slippage, hydraulic and mechanical friction. These losses can be set to a minimum with proper design.
Efficiency = Power output / power input
Let’s simplify this –
Power is billed to the customer in kilowatt hours (KWH). KWH used is determined by the input HP to the system and read at the electrical meter. The more we can reduce the KWH required, the more efficient the system, ultimately reducing the operating cost to the end user.
OPE is determined by taking the hydraulic efficiency of the pump at its operating point X the electrical efficiency of the motor, minus the losses in the system.
Let’s look at an example –
If a pump is operating at 86% hydraulic efficiency and the motor is operating at 95% efficiency, the OPE will be .86 x .95 or .81% before we add in our losses. Losses typically will be 5-6 % in a properly designed system and even more in a poorly designed system.
A OPE is 75% is considered to be high.
If we picked a pump that was 80% efficient at our design point and used the same motor, our OPE would drop to 71% (still considered good) using the same criteria a above.
Let’s look at some numbers. A system that requires 2000 GPM @ 400 feet of head with 86% bowl efficiency will use 235 bowl HP. The same conditions with 80% hydraulic eff would require bowl 253 bowl HP. That’s 18 more HP to do the same job. 18 HP / .95% (motor eff) = 14.00 KW. At .14 cents a KWH, that’s $1.96 more per hour.If we run our pump 2100 hours per year, that’s over $4000.00 per year in additional operating costs. Over 10 years that’s 40Kplus in savings for a 6% increase in hydraulic efficiency!
Efficiency pays rewards.
Electric motor efficiencies have been set by the Department of Energy (DOE), but pump efficiencies have yet to be set. Our best way to improve OPE is by picking the highest efficiency pump we can, while still meeting our design criteria. Losses in turbine pumps consist of column friction losses and shaft and thrust bearing losses. Column friction losses increase the total head required. Thrust bearing and shaft HP losses increase the load to the motor.
While in the design process for a deep well pump, we look for several factors on the pump performance curve. Obviously, we want the highest efficiency at our operating point. We also want to pick a curve that puts our operating point 1-2 % to the right of the BEP (best efficiency point on the curve).We do this for two main reasons, as the water table declines and as the pump wears, the operating point moves to the left on the curve (towards shutoff).As this happens the pump efficiency actually increases and stays efficient longer as it moves toward BEP and beyond. In deep well pumps, we also look for the steepest curve that meets our other requirements (the highest shutoff head). By selecting the steepest curves, the capacity drops off slower as the pump wears and the water table drops.
We also need to insure our column size is correct and adequate for capacity and velocity while incurring the least amount of friction losses. The same with our line shaft, it must be able to handle the HP required and be suitable for our elongation requirements while keeping our additional shaft HP to a minimum.
As I stated, motor efficiencies have been regulated by the DOE (Dept of Energy), and now must meet the premium efficiency standards set. The DOE is also setting efficiency standards for pumps which will begin to take effect in 2020. The DOE is well aware that the higher the OPE’s we have, the less energy will be consumed and need to be produced. As responsible suppliers and designers, we need to make the best selections for our customers in regards to quality and overall plant efficiencies.A well designed pump system with the highest OPE is in the best interest of all and begins to pay dividends immediately.
I will be glad to answer any questions you may have. I encourage you to contact me.
palbanese@mitchellewis.com